Marc van Moorsel from BÜHNEN and Junior Boerhave from “The Chocolate Factory” greet each like friends. It’s pretty obvious the two men get on very well together. The trade magazine “Pakkracht” had the chance to see the adhesive application system in action.
Marc van Moorsel and Junior Boerhave have a very good relationship, which is no surprise to either party: The adhesive specialist from BÜHNEN is well-known for his comprehensive advice and excellent customer service. The latter exactly underlines this customer relationship and is what has convinced the Dutch chocolate manufacturer to use the line motion control system from BÜHNEN.
Other companies blend their ingredients into the chocolate itself. Sprinkling the chocolate surface achieves a very different mouth feel and taste experience. To be quite honest, we hadn’t expected it to be so successful, but soon our chocolate bars were to be found in the shelves of the chains Jumbo and Albert Heijn."
Appreciated cooperation/collaboration
"Not so long ago, we had an adhesive-related problem in our production process”, Boerhave continues. “This had to be solved as quickly as possible. The threatening production stop would have cost us a lot of money. Many suppliers can‘t understand the time pressure. Marc came round quickly and was very helpful. We have known each other for a long time already. Due to a local warehouse store, short communication channels and no useless costs, the collaboration is very much appreciated by both parties.”
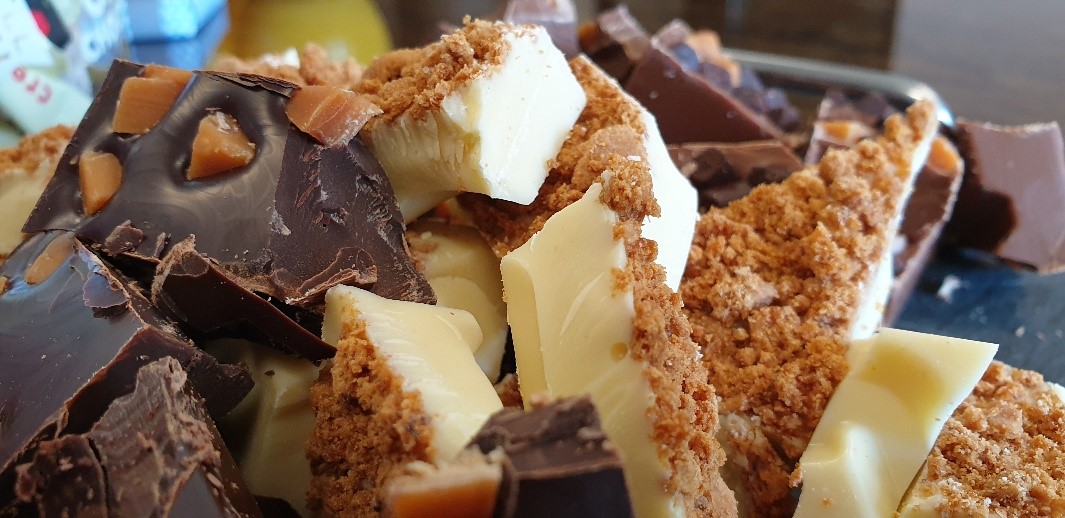
"During the past year, BÜHNEN has introduced the new line motion control system to the market and this came at exactly the right moment for the chocolate factory” says van Moorsel. "As a sales representative for BÜHNEN, I am very proud to be able to supply the company. Here we have installed the adhesive tank system HB 6000, the application head HB 20 and the module, as well as the brand new line motion control system. This system combination ensures that the minimum amount of adhesive can be applied. Using this application, even the smallest amount of hot melt adhesive was sufficient."
Important note
Naturally, we have deliberated in length and intensively as to which adhesive should be used for the packaging of the chocolate bars. “I didn’t know precisely how hot melt adhesive worked“, says Boerhave and admits: “I just thought: If it doesn’t stick we have to apply more adhesive. But that‘s not the case. Luckily, Marc had advised and trained us well, in that he explained the basic principles of hot melt during individual adhesive training.”
It goes without saying that, in a chocolate factory, it has also to be taken into account that packaging and bonding of foodstuffs must comply with the strict regulations. “One cannot simply use just any adhesive”, says Van Moorsel. “If, for any reason, this adhesive comes into contact with the chocolate, one does not want anybody to become sick by consuming the chocolate. The hot melt adhesive used meets FDA (Food and Drug Administration) regulations and conforms to the strict guidelines for packaging of foodstuffs." Boerhave added: "These are the most important areas where one doesn’t want to take any chances, and where the advice of an expert like Mark is so valuable.”
Line motion control system with touchscreen
At the end of the impressive Johnny Doodle chocolate bar production line is the automatic packaging machine, which folds the foils around the bars and places them in paper packaging. In order to glue the packaging, a hot melt adhesive tank system is available, in combination with the line motion control system.
This control system enables automated working. The solenoid valves on the application head of the peripheral device are controlled independently of each other, thus enabling precise and reproducible hot melt adhesive application. This application is carried out by calling up so-called recipes or programme variants which have been programmed for The Chocolate Factory.
The recipes simplify the speedy exchange of the packaging to be bonded in the production line. Up to one hundred recipes can be programmed. The line motion control system is operated via an integrated touchscreen. “The touchscreen is completely new and can be used for countless settings. This makes it possible to automate the entire bonding process. In addition, up to four additional application heads can be connected. A lot of hot melt adhesive can be saved with the line motion control system”, explains van Moorsel.
"Hygiene has high priority at BÜHNEN. We achieve this at our customer’s by protecting the hot melt adhesive bags from dust and storing them dry in large containers. This prevents contamination with foreign bodies”.
New start for Johnny Doodle
The line motion control system is, however, not the only innovation at The Chocolate Factory. The chocolate bars and the packaging have also been renewed.
“We thought it was a pity that the old packaging didn’t show what beauty was inside. That is why we present half of the bar through a recess in the new packaging”, says Boerhave.
“I was also involved in the development of the new packaging”, laughs van Moorsel. "The adhesion of the adhesive also depends on the surface to be bonded. For this reason I recommended a special surface pen. It can be used to measure whether each new surface can be bonded”. The chocolate factory is more than satisfied with this commitment and service.
“I really like the fact that BÜHNEN even wanted to help develop the relaunch. I very much appreciate the fact that they think with us. In my opinion, this reflects our good relationship”, concludes Boerhave.